Crimp Pin Connectors: The Backbone of Reliable Electrical Connections
- mblassd
- Nov 22, 2024
- 5 min read
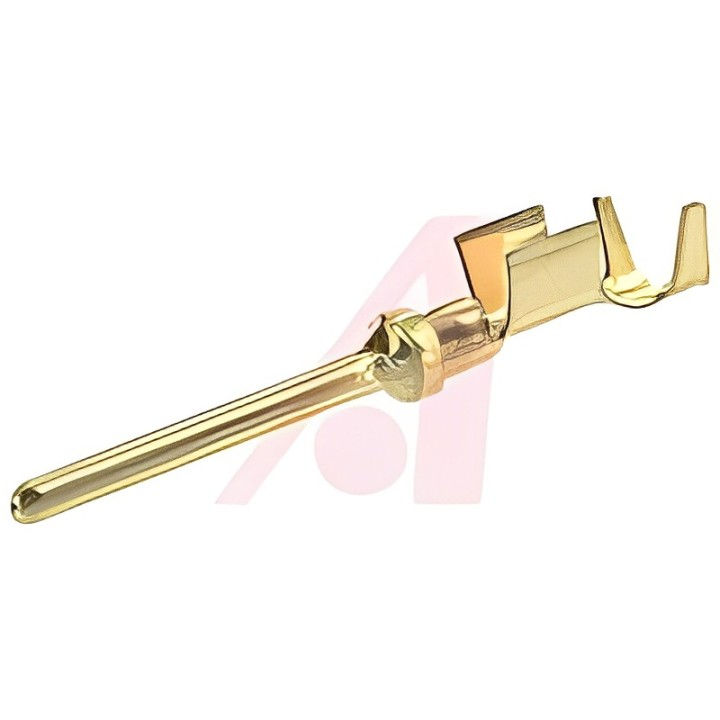
Crimp pin connectors are essential components in the world of electronics and electrical engineering. These connectors ensure robust, secure, and efficient electrical connections between wires and devices. From consumer electronics to industrial applications, their versatility and reliability make them a popular choice for professionals and hobbyists alike. In this article, we’ll explore crimp pin connectors in detail, delving into their structure, applications, types, advantages, and best practices for installation and maintenance.
Introduction to Crimp Pin Connectors
Crimp pin connectors are devices used to terminate wires by joining them to terminals or other connectors through a process called crimping. Crimping involves compressing a metal sleeve (the crimp) onto a wire using a specialized tool. This mechanical connection provides electrical conductivity and mechanical stability, ensuring a secure bond without the need for soldering.
The primary purpose of crimp pin connectors is to establish reliable electrical connections in various applications, including automotive, aerospace, telecommunications, and consumer electronics. Their ability to deliver consistent performance in high-vibration and high-temperature environments makes them indispensable in modern technology.
Key Components of Crimp Pin Connectors
Crimp pin connectors consist of the following main components:
Pin or Terminal:The metal pin is the actual conductor that interfaces with other components. Pins are typically made from conductive materials like copper or brass, often plated with gold, silver, or tin to improve conductivity and resist corrosion.
Insulation Barrel:Surrounding the wire connection, the insulation barrel helps secure the insulation of the wire and prevents accidental short circuits.
Crimp Barrel:This section of the connector is compressed during the crimping process to form a secure mechanical and electrical connection with the wire.
Housing or Connector Body:The housing protects the pins and ensures proper alignment when mated with a corresponding connector. It can be made of plastic or metal, depending on the application.
Types of Crimp Pin Connectors
Crimp pin connectors come in a variety of designs to suit different applications. Some common types include:
1. Ring Terminals
These are circular connectors used to connect wires to screws or studs. They are commonly found in automotive and industrial wiring.
2. Fork Terminals
Shaped like a fork, these connectors allow easy installation on screws or terminals without completely removing the screw.
3. Blade Terminals
These flat, rectangular connectors are widely used in automotive and appliance wiring.
4. Butt Connectors
Designed for splicing wires, butt connectors allow two wires to be joined end-to-end securely.
5. Pin Terminals
These connectors have a pin-shaped end, making them suitable for insertion into terminal blocks or other similar connectors.
6. Male and Female Crimp Terminals
These connectors are designed to mate with each other, forming a plug-and-socket connection. They are widely used in modular systems.
Advantages of Crimp Pin Connectors
Crimp pin connectors are preferred over other types of connectors for several reasons:
1. Ease of Installation
Crimping is a straightforward process that doesn’t require heating or soldering, making it faster and safer.
2. Reliability
Properly crimped connections are highly reliable, offering excellent resistance to vibration, temperature fluctuations, and corrosion.
3. Consistency
When performed with the correct tools and techniques, crimping ensures consistent results across multiple connections.
4. Versatility
Crimp pin connectors are available in various sizes, materials, and designs, making them suitable for diverse applications.
5. Cost-Effectiveness
Compared to soldered connections, crimping is less labor-intensive and doesn’t require expensive materials, reducing overall costs.
6. Durability
Crimped connections are less prone to failure over time, ensuring a longer lifespan for the overall system.
Applications of Crimp Pin Connectors
Crimp pin connectors are used across numerous industries due to their reliability and adaptability. Some key applications include:
1. Automotive Industry
Crimp pin connectors are commonly used in vehicle wiring systems to ensure secure connections in high-vibration environments.
2. Aerospace and Defense
In aircraft and defense systems, crimp pin connectors are critical for maintaining reliable connections under extreme conditions.
3. Consumer Electronics
From household appliances to computers, crimp pin connectors are integral to ensuring efficient electrical connections in compact spaces.
4. Telecommunications
In communication systems, these connectors play a vital role in transmitting signals with minimal interference.
5. Industrial Automation
Crimp pin connectors are essential in machinery and control systems, where reliability and precision are paramount.
6. Renewable Energy Systems
Solar panels and wind turbines use crimp pin connectors to facilitate secure connections in harsh outdoor environments.
How to Choose the Right Crimp Pin Connector
Selecting the appropriate crimp pin connector is crucial for ensuring optimal performance. Consider the following factors:
Current and Voltage Ratings:Ensure the connector can handle the electrical load of the application.
Wire Size Compatibility:Choose a connector that matches the gauge of the wire.
Material and Plating:Opt for connectors made from materials that resist corrosion and offer good conductivity.
Environmental Conditions:For outdoor or harsh environments, select connectors with weatherproof or rugged designs.
Mating Requirements:Ensure the connector is compatible with the corresponding mating part.
Certifications and Standards:Look for connectors that meet industry standards like UL, CE, or RoHS.
Best Practices for Crimping
Achieving a secure and reliable connection requires proper crimping techniques. Here are some best practices:
1. Use Quality Tools
Invest in a good-quality crimping tool designed for the specific type of connector.
2. Strip the Wire Correctly
Strip the wire to the appropriate length without damaging the conductor strands.
3. Insert the Wire Properly
Ensure the wire is fully inserted into the crimp barrel before applying pressure.
4. Apply the Correct Force
Use the right amount of force during crimping to avoid over-compression or under-compression.
5. Inspect the Connection
After crimping, visually inspect the connection to ensure it is secure and free of defects.
6. Test the Connection
Perform a pull test to verify the mechanical strength of the crimp.
Common Issues and Troubleshooting
Despite their reliability, crimp pin connectors can face issues if not installed correctly. Here’s how to address some common problems:
1. Loose Connections
Check if the wire is fully inserted and the crimping force was sufficient.
2. Corrosion
Use connectors with corrosion-resistant plating and ensure proper insulation.
3. Overheating
Verify that the connector is rated for the current and voltage of the application.
4. Wire Damage
Avoid over-stripping the wire or using tools that can damage the strands.
Future Trends in Crimp Pin Connector Technology
As technology advances, crimp pin connectors are evolving to meet new challenges. Emerging trends include:
Miniaturization:Smaller connectors are being developed to cater to compact electronic devices.
Smart Connectors:Advanced designs incorporate sensors to monitor connection quality and detect faults.
Eco-Friendly Materials:Manufacturers are exploring sustainable materials to reduce environmental impact.
High-Speed Data Transmission:Connectors are being optimized to support faster data rates for modern communication systems.
Conclusion
Crimp pin connectors are vital components in modern electrical and electronic systems. Their ability to provide secure, reliable, and efficient connections has cemented their role in various industries. By understanding their types, applications, and installation techniques, engineers and technicians can leverage these connectors to create robust and durable systems. As technology progresses, crimp pin connectors will continue to evolve, meeting the demands of future innovations while maintaining their legacy of reliability and performance.
Comments