Hydraulic Pressure Relief Valve: An In-depth Overview
- mblassd
- Oct 4, 2024
- 5 min read
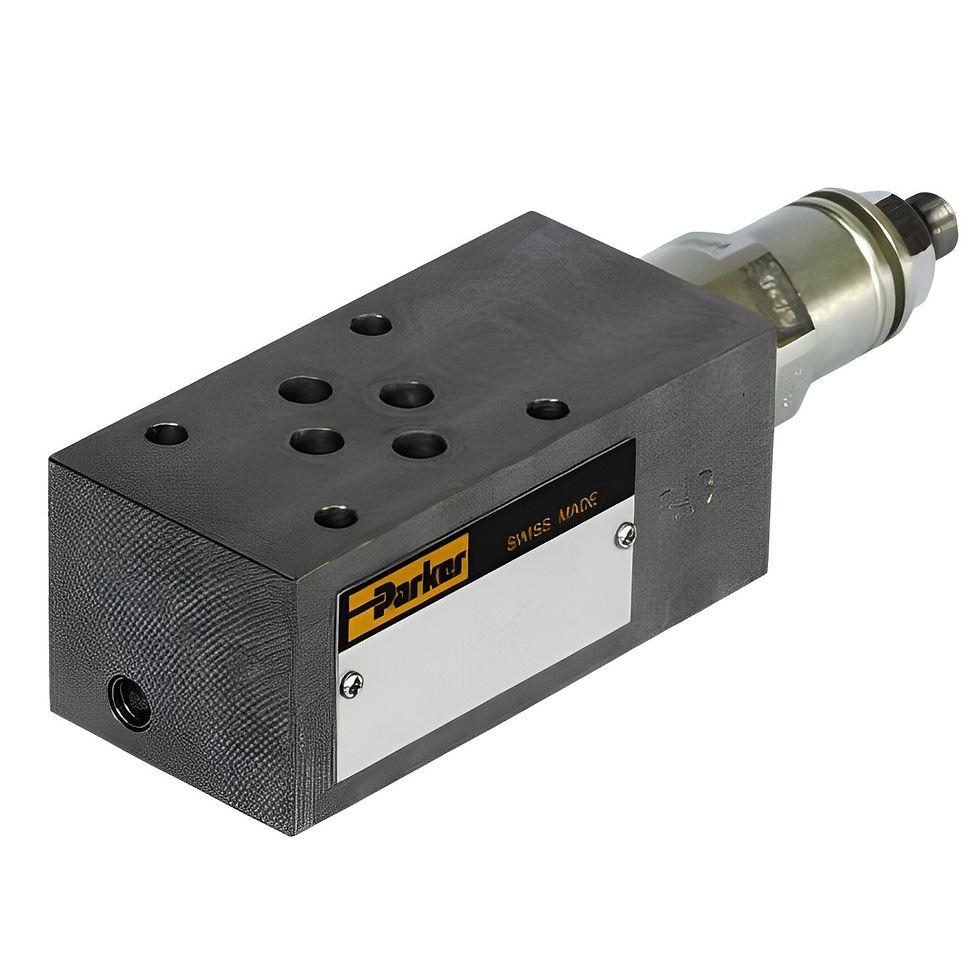
Introduction to Hydraulic Pressure Relief Valves
Hydraulic systems are widely used in a variety of industries due to their ability to efficiently transfer energy, exert large forces, and manage heavy loads. These systems rely on hydraulic fluid to transmit power. To maintain safety and performance, hydraulic systems must control and limit the pressure generated by the hydraulic pump. One of the key components responsible for this task is the
hydraulic pressure relief valve.
A hydraulic pressure relief valve serves as a safety device that regulates or limits the pressure in a hydraulic system. Without a properly functioning pressure relief valve, hydraulic systems can experience overpressure, leading to damage or catastrophic failure. In this article, we will delve into the workings, types, applications, benefits, and maintenance of hydraulic pressure relief valves.
What is a Hydraulic Pressure Relief Valve?
A hydraulic pressure relief valve is a device designed to protect hydraulic systems from experiencing pressures higher than they are rated for. These valves ensure that the system operates within the designed pressure range, thereby protecting components such as pumps, actuators, hoses, and seals from excessive pressure.
In normal operation, hydraulic systems maintain a certain pressure to function properly. However, several factors, such as system blockages or malfunctions, can lead to pressure spikes. The pressure relief valve steps in by diverting excess hydraulic fluid when pressure exceeds the preset limit, returning it to the reservoir or a low-pressure area to prevent damage.
The Working Principle of Hydraulic Pressure Relief Valves
Hydraulic pressure relief valves operate based on a simple yet effective principle. The valve is typically set to a predetermined pressure limit. When the pressure in the hydraulic system rises beyond this limit, the valve opens to divert fluid away from the system, relieving the excess pressure.
The key components involved in the operation of a pressure relief valve include:
Inlet Port: Where the pressurized fluid enters the valve.
Valve Seat: The component that blocks fluid flow when the valve is closed.
Spring or Actuator: Determines the set pressure by applying force to the valve seat.
Outlet Port: Where the relieved fluid exits the valve and returns to the reservoir.
Under normal conditions, the valve remains closed, and fluid flows through the system unimpeded. When system pressure exceeds the set point, the force generated by the hydraulic fluid overcomes the force exerted by the spring. This causes the valve to open, allowing fluid to flow out of the system, reducing pressure to safe levels. Once the pressure drops to the desired range, the valve closes, restoring normal operation.
Types of Hydraulic Pressure Relief Valves
There are several types of hydraulic pressure relief valves, each designed for specific applications and performance requirements. The most common types include:
1. Direct-Acting Pressure Relief Valves
Direct-acting pressure relief valves are simple and cost-effective. These valves use a spring-loaded mechanism to open when system pressure exceeds the preset level. The valve opens directly under the force of the fluid pressure, allowing excess fluid to bypass or return to the tank. They are commonly used in systems with lower pressure ratings.
2. Pilot-Operated Pressure Relief Valves
Pilot-operated pressure relief valves are more complex than direct-acting valves and are designed for systems that operate under higher pressures. These valves consist of a main valve and a pilot valve. The pilot valve controls the operation of the main valve, making the system more responsive to pressure changes. Pilot-operated valves provide better performance, accuracy, and stability under varying load conditions, making them ideal for high-pressure systems.
3. Adjustable Pressure Relief Valves
Adjustable pressure relief valves allow operators to manually adjust the pressure setting as needed. This flexibility is useful in systems that experience varying pressure demands. The adjustable design makes them versatile for different applications, such as in industrial machines or mobile hydraulic equipment.
4. Proportional Pressure Relief Valves
Proportional pressure relief valves operate in a way that the valve opening is proportional to the system's pressure. This allows for precise pressure control, reducing energy loss in hydraulic systems. These valves are electronically controlled, making them suitable for applications requiring precise pressure modulation.
5. Cartridge Pressure Relief Valves
Cartridge-style pressure relief valves are compact and often used in custom hydraulic manifold assemblies. These valves are designed to fit into a cavity and are commonly used in mobile or space-constrained applications. Their compact design allows for integration into smaller systems without sacrificing performance.
Applications of Hydraulic Pressure Relief Valves
Hydraulic pressure relief valves are essential in numerous applications across a wide range of industries. Some of the most common applications include:
1. Industrial Machinery
In industrial manufacturing, hydraulic systems power a variety of machines and tools. Pressure relief valves ensure that these machines operate safely by maintaining pressure within the designed limits. This prevents damage to expensive equipment and ensures smooth, uninterrupted production.
2. Construction and Agricultural Equipment
Hydraulic systems are prevalent in construction and agricultural machinery such as excavators, tractors, and loaders. Pressure relief valves protect these machines' hydraulic circuits from overpressure, ensuring the longevity of the equipment and the safety of the operators.
3. Aerospace and Aviation
In the aerospace industry, hydraulic systems are critical for controlling flight surfaces, landing gear, and braking systems. Pressure relief valves are integral to maintaining precise hydraulic pressure, ensuring the safe operation of aircraft components under varying flight conditions.
4. Automotive Industry
In vehicles, hydraulic systems are used for braking, steering, and transmission. Pressure relief valves prevent pressure surges that could damage these systems or lead to malfunction, ensuring reliable vehicle performance.
5. Hydraulic Power Units (HPUs)
Hydraulic power units, which are standalone systems providing power to hydraulic machinery, depend on pressure relief valves to regulate system pressure. These valves ensure the smooth operation of multiple hydraulic circuits within the unit.
Benefits of Hydraulic Pressure Relief Valves
Hydraulic pressure relief valves offer a range of benefits, making them indispensable in various applications. These include:
1. Enhanced Safety
The primary purpose of pressure relief valves is to prevent dangerous overpressure situations that could lead to system failure, leaks, or ruptures. By automatically relieving pressure, they protect both personnel and equipment from harm.
2. Extended Equipment Life
Excessive pressure can wear down hydraulic components, leading to frequent repairs or replacements. By maintaining system pressure within the optimal range, pressure relief valves reduce wear and tear on components, extending the life of the equipment.
3. Improved System Efficiency
Relief valves allow systems to operate efficiently by preventing pressure buildup. This reduces energy waste, ensuring that hydraulic power is directed towards productive tasks rather than managing excessive pressure.
4. Cost Savings
By protecting hydraulic systems from damage, pressure relief valves help reduce the frequency of breakdowns and maintenance costs. They also reduce downtime, which can be costly in industries like manufacturing, where productivity is crucial.
Maintenance and Troubleshooting of Hydraulic Pressure Relief Valves
Regular maintenance of hydraulic pressure relief valves is essential to ensure they continue to operate efficiently. Some maintenance practices include:
1. Inspecting for Leaks
Leaks around the valve area can indicate wear or damage to seals. Regular inspection of the valve and its surrounding components is necessary to prevent system inefficiencies.
2. Checking Pressure Settings
Over time, the pressure settings on adjustable valves may drift or require recalibration. Operators should regularly verify that the valve is set to the correct pressure to prevent malfunctions.
3. Cleaning Valves
Contaminants in hydraulic fluid can cause valve blockages or damage. Routine cleaning of valves, filters, and hydraulic fluid helps prevent such issues, ensuring the system remains operational.
4. Testing Valve Functionality
Periodically testing the relief valve's functionality ensures that it opens and closes as needed during overpressure events. If the valve fails to open under excess pressure, it should be repaired or replaced immediately.
Conclusion
Hydraulic pressure relief valves are crucial components in maintaining the safety and efficiency of hydraulic systems across many industries. By regulating system pressure, these valves prevent overpressure situations that could lead to equipment damage or failure. Understanding the types, applications, and maintenance of hydraulic pressure relief valves is essential for anyone working with hydraulic systems. Investing in high-quality valves and performing regular maintenance ensures the longevity and reliability of hydraulic machinery, safeguarding both personnel and assets.
Comments