Unveiling the Fundamentals: A Deep Dive into Plummer Blocks and Pillow Blocks
- mblassd
- Nov 21, 2024
- 3 min read
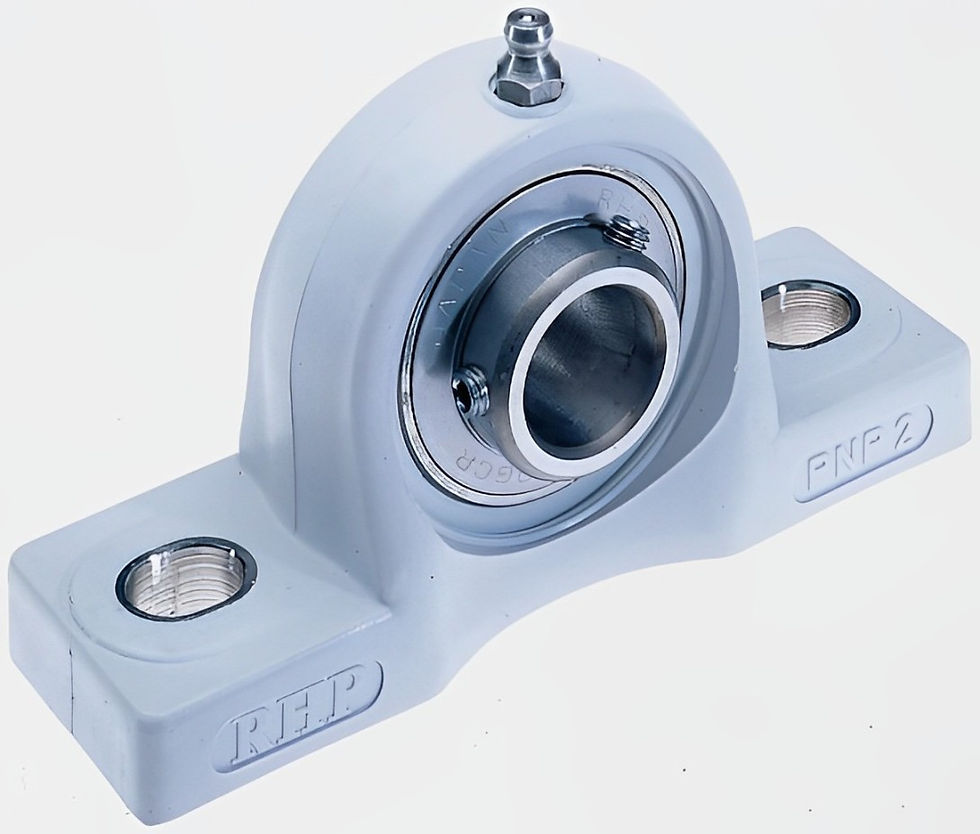
Introduction
In the world of mechanical engineering, bearings play a pivotal role in facilitating smooth rotational or linear movement between two parts. Among the various types of bearings, Plummer blocks and pillow blocks stand out due to their unique design and widespread applications. This article explores the intricacies of Plummer blocks and pillow blocks, discussing their designs, functionalities, and industrial applications.
Understanding Plummer Blocks
Definition and Design
Plummer blocks, also known as split bearing housings, are robust structures designed to provide a high-strength housing for bearings. These blocks are typically made from cast iron or cast steel, providing excellent durability and resistance to heavy loads and environmental challenges. The defining feature of a Plummer block is its split design, allowing for easy assembly, inspection, and maintenance of the bearings housed within.
Components of a Plummer Block
A typical Plummer block includes several key components:
Base: The main structure that supports the entire assembly.
Cap: Fits on top of the base and is bolted down to secure the bearing in place.
Bearing Housing: Encloses the bearing and is usually split horizontally to ease the process of bearing replacement.
Seals: Protect the bearing from dust, dirt, and moisture, extending the life of the bearing.
Adapter Sleeve: Facilitates the secure fit of the bearing on the shaft.
Applications
Plummer blocks are indispensable in applications requiring the support of high radial and axial loads. They are commonly used in conveyor belts, large-scale fans, rotary kilns, and within the mining and construction industries. Their ability to withstand tough environments makes them ideal for heavy-duty applications.
Exploring Pillow Blocks
Definition and Features
Pillow blocks, also known as plummer blocks in some regions, are pedestal-mounted bearing housings and are a subtype of the more extensive bearing housing category. Unlike Plummer blocks, pillow blocks contain bearings that are typically encased in a housing that mounts to a surface through the base of the block.
Components of a Pillow Block
Pillow blocks consist of:
Housing: Generally made from cast iron or pressed steel.
Bearing: Ball, roller, or sleeve bearings are common types used within pillow blocks.
Locking Mechanism: Ensures the bearing is securely fastened to the shaft, often via set screws or a locking collar.
Applications
Pillow blocks are widely used in applications involving lighter loads and where alignment is crucial. They find applications in agricultural machinery, conveyance systems, and light manufacturing equipment. The simplicity of their design and ease of maintenance make them popular choices for a variety of applications.
Comparison between Plummer Blocks and Pillow Blocks
While both Plummer blocks and pillow blocks serve similar functions, they differ significantly in design and suitability for specific applications. Plummer blocks are better suited for high load capacities and environments where split housings facilitate maintenance without disturbing the entire assembly. In contrast, pillow blocks are favored in applications where space is limited and installation simplicity is prioritized.
Installation and Maintenance Tips
Installation
Proper installation is crucial for the optimal performance of both Plummer and pillow blocks. It involves:
Ensuring the shaft and housing are clean and free of debris.
Aligning the shaft correctly to avoid undue stress on the bearings.
Securing the bearings and applying the right amount of lubricant.
Maintenance
Regular maintenance ensures longevity and reliability, encompassing:
Regular inspection for wear and tear.
Timely replacement of seals and bearings.
Monitoring lubrication levels and quality.
Conclusion
Plummer blocks and pillow blocks are fundamental components in the mechanics of rotational and linear movements in various industrial settings. Understanding their designs, applications, and maintenance needs can significantly enhance equipment efficiency and lifespan. By selecting the appropriate type of bearing housing and adhering to proper installation and maintenance practices, industries can achieve optimal machinery performance, resulting in increased productivity and reduced downtime.
Comments